Home » Posts tagged 'steel fabrication'
Tag Archives: steel fabrication
Recent Comments
The Basics of Welding
Welding Boise Idaho is a skill that opens up a world of possibilities, whether it’s for home projects or a career path. It starts with understanding how welding works and then learning to perform it properly.
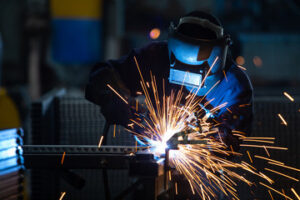
Start by preparing your metal surfaces and be sure to use a wire brush to remove contaminants. Make sure your welder’s settings are dialed in based on the thickness of the material you’re working with.
Welding requires high heat to melt the filler material and join the materials together. This high heat also affects the surrounding base metal, resulting in the formation of the Heat Affected Zone (HAZ). The HAZ may become weaker or more brittle compared to the rest of the base material, which can lead to stress concentration points and potential flaws. The size and severity of the HAZ is dependent on a variety of factors, such as welding technique and material properties.
Welders can control the size of the HAZ by lowering the temperature during welding. High temperatures cause varying effects on the microstructure of the base and weld metals, and this is especially true for the region near the fusion line. The high temperatures in the HAZ can cause changes to the atomic structure of the base metal, which can result in reduced strength and corrosion resistance.
The size of the HAZ is also affected by the type of filler material used during welding. Welding with a filler metal that has similar properties to the base metal can help minimize these effects. In addition, selecting a low-melting point filler metal can reduce the amount of heat transferred to the base material during welding, which will reduce the size of the HAZ.
Another factor that influences the size of the HAZ is the cooling rate in the weld area. A weld with a slow cooling rate will have a smaller HAZ than a weld with a fast cooling rate. This is because the slower cooling rate allows the metal to cool at a more gradual rate and avoids localized hot spots.
The cooling rate in the HAZ also affects how much the weld metal expands and contracts. Welds with a higher rate of expansion will have a larger HAZ than welds with a lower rate of expansion. The rate of expansion and contraction in the weld metal is also affected by the material’s thermal conductivity, which can impact the time it takes for the weld to reach equilibrium with the base metal. In addition, the choice of electrodes can also affect the rate of expansion and contraction in the weld area.
Pressure
During welding, pressure is applied when electrodes connect to workpieces. This pressure is what controls the generation of heat, affecting the quality and strength of a weld. It also helps to break through surface layers that may be coated with contaminants or coatings, ensuring a clean and contaminant-free welding interface.
The pressure used in welding can vary depending on the material and the thickness of the workpieces. For example, a thicker workpiece will require more pressure to achieve proper penetration and fusion. A thinner workpiece can be welded at lower pressures, as the arc will not need to travel as far to reach the base metal.
When working with resistance spot welding machines, pressure control is important because it influences the weld quality. For this reason, it’s critical to use a system that can automatically adjust the welding pressure. This will ensure optimal electrode contact, minimized material deformation, and less electrode wear.
A pressure control system will help ensure that the welds produced meet industry standards and specifications. It will also improve the efficiency of welding operations, allowing workers to complete projects more quickly and accurately. Moreover, the right pressure control system will help to prevent distortion in some welding applications, such as joining dissimilar materials or materials with varying thicknesses.
Welding is a demanding profession that requires a high level of precision and specialized knowledge. It also demands physical strength and endurance, as welders often have to lift heavy loads, operate machinery, and work in harsh environments. In addition, the job requires good hand-eye coordination and manual dexterity to handle tools and equipment.
Despite the challenges, a career as a welder can be very rewarding. Welders are in demand across industries, and there are many different opportunities to advance within the field. With sufficient experience, you can become a welding foreman, supervisor, or workshop manager. Alternatively, you can specialize in a particular area of welding such as aluminium or stainless steel welding. Additionally, you can also choose to work independently as a freelance welder or start your own welding business. In this way, you can be in charge of your own destiny and create a career that’s both satisfying and flexible.
Oxygen
Welding requires a high level of concentration and precision. As a result, welders must follow strict safety protocols in order to protect themselves and their work environment from potential hazards. In addition, welding is physically demanding, requiring extensive use of muscles and joints. This can lead to fatigue, which may increase the risk of error.
Welders can protect themselves by using a protective atmosphere, which prevents contaminants from entering the weld area. Common shielding gases include carbon dioxide, hydrogen, argon and nitrogen. Inert gas mixtures are also available, which combine a number of these gases in specific ratios to improve the performance of the welding process.
For example, helium is ideal for welding metals like aluminum because it has a lower density than air and can therefore be used at higher voltages. When mixed with argon, helium creates a stable arc that allows for consistent heat input and penetration.
However, there are some negative effects of oxygen on welding. It can cause a negative effect on the transient thermal behavior and microstructure of the molten pool, which leads to poor weld quality. It can also lead to brittle intermetallic compounds and an asymmetric weld pattern. It can also affect the dilution phenomenon and the correlation between the dilution and convection flow.
Oxygen is also a contaminant in welding because it can react with chromium and iron to form poisonous oxides. These can irritate the eyes, skin and respiratory system, and some are suspected carcinogens. Chromium is found in stainless steel and some high-alloy materials, as well as welding rods. It converts to hexavalent chromium during welding, which can cause a number of health problems including eye, skin and respiratory irritation, and lung issues such as emphysema and bronchitis. It can also affect the bones and kidneys.
Shielding Gas
While many factors affect welding, the shielding gas used is among the most important. This gas protects the molten weld pool from atmospheric contaminants, which can cause weld defects such as porosity, cracking and nitriding. It also helps control the arc characteristics, such as arc stability and spatter levels, which can impact production speed.
Shielding gas selection depends on the weld material, thickness and process. For example, low-alloy and some stainless steels benefit from a higher concentration of argon in the shielding gas because it promotes better heat transfer and penetration. On the other hand, aluminium welding requires a mixture with less argon and more oxygen to prevent oxidation and achieve good weld appearance and corrosion resistance.
In addition, the type of gas can influence weld puddle characteristics, such as fluidity and hardness. Some gases can even change the microstructure of the weld, especially if they are added to the filler metal. For instance, nitrogen can be added to duplex stainless steels to improve pitting resistance and create a balanced austenite/martensite microstructure in the weld.
The shielding gas also has an effect on the mechanical properties of the weld metal and HAZ. For example, the use of CO2 to shield the arc produces higher weld strengths but may result in poor toughness in the weld metal and HAZ.
Argon/CO2 mixtures are typically recommended for most applications, but the exact composition varies depending on the application. The ideal mix varies between 75-95% argon and 5-25% CO2. The appropriate blend for your application will depend on your desired weld specifications, production requirements and cleaning requirements.
It is also important to note that the gas blend can have an effect on the weld bead shape, width and depth. For example, argon/CO2 mixes with a high ionization potential tend to produce wider weld bead diameters than those with a lower ionization potential like carbon dioxide or nitrogen. In addition, the shielding gas can affect the depth of penetration, with higher ionization potentials such as argon producing deeper penetration than carbon dioxide or nitrogen.
Categories
- Beauty Care
- Body Essentials
- Boiler Services
- Car Services
- Cleaning Services
- Construction
- Deck Repair Services
- Dental Services
- Garage Services
- General Contractor
- Gutter Services
- Home Improvement
- Home Services
- HVAC
- Insulation
- Lawyer
- Metal Fabrication Services
- Military Car
- Mold Removal
- Movers
- Painting Contractor
- Pest Control
- Plumbing
- Roofing
- SEO
- Septic Tank
- Strategy Workshops
- Tree Services
- Uncategorized